When it comes to joints, no one can beat orbital welding. With orbital welding, you’re able to produce high-quality joint solutions that are secure, fast, and easy to finish.
Mass production will position your business higher in the welding marketplace. According to research, the market for welding products is growing at a 10% compound growth rate.
Therefore, understanding the orbital welding process is vital.
[convertkit form=3197073]What is Welding
Welding is one of the most common manufacturing processes in modern industry. It is affordable and, when done correctly, gives the best possible results.
It is the process of “joining” metal pieces by causing the coalescence of two into a single metal mass called a “weld.” Also, there is plastic welding, especially when making motherboards and circuits.
It is an ancient practice that dates back to 3000 BC, although there have been changes in techniques. Modern welding was developed during World War II to join aluminum aircraft parts quickly.
The basics of the welding process were forged into shape by the 1940s and are still in use today. Welding is via various methods and machines, but most types of welding use simple concepts: of joining together.
What is Orbital Welding
Orbital welding is a special type of arc welding in which the arc is rotated mechanically through 360 degrees inside a circular weld joint. The process uses a set of power supplies, controls, and other equipment to make an orbital weld.
Because the weld head rotates around the pipe or tube, welders can use it to join parts that other methods can’t. Orbital welding is common in the industries. The process most commonly uses heat from an electric arc under computer control.
Roderick Rohrberg developed the orbital tig welding technique in 1960 to improve rocket hydraulic and fuel leakages.
Today’s orbital welders are highly-refined pieces of equipment with sophisticated controls that allow for nearly flawless welds each time a technician uses them.
Types of Equipment for Orbital Welding
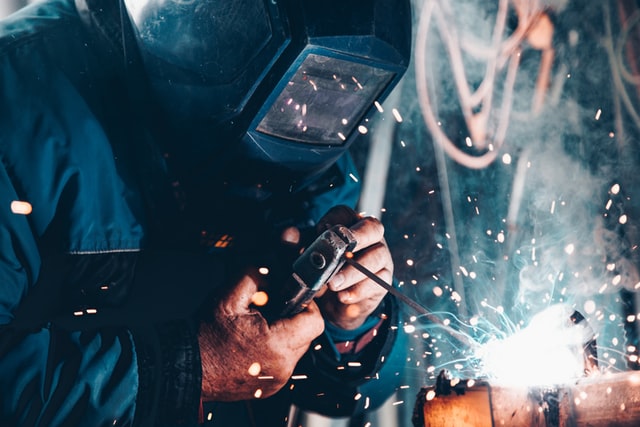
Photo by Rob Lambert on Unsplash
The orbital welding process is different from traditional welding. In this process, the filler wire travels in an orbital path while the tube remains stationary. This process is advantageous as it helps welders achieve superior quality welds and improves productivity.
The four primary tools for orbital welding are:
Programmable Power Supply
The power supply is attached to the weld head and plays a crucial role in providing the current needed for the arc welding process.
The power supply must generate sufficient energy to aid in the welding process. It allows you to set various parameters for different welding operations, such as current type (constant current or constant voltage), frequency, and voltage.
Connection wire
This cord connects the TIG torch to the power supply unit linked to a programmable controller.
You must handle the cable carefully for safety. Unlike flux core wires, this cable has a very high voltage.
Welding heads
Depending on the needs of a job, some of the heads include internal, external, micro-miniature, variable angle, and more. You must choose the right type of head for each project to achieve the desired results.
Welding heads are attached to a rotary motion device that spins them around in a circular motion of about 180 degrees or more during orbital welding. Welding heads are available in various sizes depending on the diameter of the pipe or tube you’re welding.
Cooling system
The coolant system is essential in protecting the weld from thermal damage. Without the coolant, the heat from welding can quickly ruin a job.
How Orbital Welding process works
Orbital welding is a manual process with a computer-controlled torch that you can customize to create different products. The operator sets up the machine by inputting all necessary parameters into the control panel, such as the filler metal type, torch angle, speed, etc.
The machine then automatically creates the weld based on these parameters.
An orbital welding machine has an internal rotating mechanism around a stationary workpiece. The tool moves around its circumference to create a perfect weld with each rotation.
The torch has a constant orientation with respect to the tube centerline throughout the weld cycle. Orbital welding machines are available in several sizes depending on the pipe or tube diameter. The smallest machines weld pipes as small as 1/8″ in diameter.
Uses of Orbital welding
Nuclear piping
Orbital welding is helpful for nuclear piping for its extreme precision when creating these pipes. The fusion welds on nuclear piping must be highly reliable and structurally sound. The government highly regulates nuclear pipes for use in a harsh environment.
Pharmaceuticals
In pharmaceuticals, orbital welding helps make a hygienic, sterile connection. The process makes completely smooth, seamless joints that you can then polish to a mirror-like finish. The process is usually quick and efficient.
Aerospace
Orbital welding processes solid and durable parts that withstand harsh environments. Aerospace industries use this technology to make welds that withstand high temperatures or very low pressures. These parts must also be very light not to weigh down the aircraft or spacecraft.
Advantages of Orbital Welding
It’s clean and efficient.
Orbital welding is a clean, consistent and efficient method for welding. There’s no need for filler material, so it saves time and money.
It also avoids spattering.
The process is entirely automated, so the welder doesn’t have to keep an eye on it during the entire process. The welder can begin working on another project while the machine works on the first one.
A significant advantage of orbital welding is that it produces welds that would be very difficult to achieve manually.
It produces Quality Welds.
There’s no need to worry about human error or fatigue with orbital welding because the process is fully automated.
It also controls heat input, creating a more consistent bead with less distortion than manual methods.
Plus, by removing the human element from the equation, there’s no need to worry about contamination from oils or other materials that can affect the integrity of a weld and lead to corrosion issues down the road.
Solves Unique Problems
Orbital welding also solves unique problems that could arise when using other methods of welding such as TIG or MIG welding.
The flexibility of orbital welding makes it possible to solve a wide variety of problems with an equally wide variety of solutions.
Disadvantages of orbital welding
Needs costly equipment:
Depending on the application, the orbital welding process needs a lot of specialized and expensive equipment—the equipment targets industrial use and not the usual money-making home projects.
The items cost an arm and leg. But, the machine is worth it. Just rent one.
Needs proper training:
Orbital welding is not an easy job to learn and practice. It requires detailed training and expertise in the field of orbital welding.
Conclusion
Various industries widely use the Orbital Welding process. Its positive-negative features influence the market and make it an essential strategy for different purposes.
The Orbital Welding process has applications in many fields, meaning there is room for expansion.