Let’s admit it – sometimes solder is just not solid enough to bond two parts, especially when you work with wires and electronics. A solder-based only solution can affect a poorly made joint with bridged pins or no joints at all, or create voids in the solder bond.
That is where solder flux comes in. Think of flux as the “magnet” that attracts the solder to the part.
Without it, the solder will not stick to what you want.
After selecting the proper temperature level and flux, even a soldering beginner can manage soldering with electronics. Flux helps remove the oxidation, cleans and aids in forming the metallurgical bond between the parts. The flux agent stays on the metallic surfaces as you apply the soldering iron.
This allows the two surfaces to form a solid and even bond.
Types of Flux for Soldering Electronics
It isn’t enough to just use any flux agent to solder wires and electronics. As an owner of SolderingIronGuide, I went through many types during my jobs. So, I can say for sure what flux agents to pick and what to avoid when you need to solder to joints or parts together.
What types of flux should you buy:
- Any flux based on rosin cores is the best pick for electronic works. It dissolves better at low levels of temperature, compared to other types. It is also better for a many delicate wiring projects. Using soldering flux with a slim rosin inner core will help to cover the wires in the best way possible;
- Leaded solders flux with a solid core are also good. Such products oxidize easier and hold a strong bond much longer. Make sure to wash your hands when working with any leaded solder; You should never need to touch solder anyway, use a bench dispenser role and pull it out with tweezers.
- Rosin flux products are based on refined pinesap. Some producers combine different rosin fluxes to deliver the greatest performance of their flux agents. Such products flow smoothly (when hot) and they remove oxides faster. When rosin flux is liquid it is acid, but when cooling down it gets more solid. That’s why consider eliminating the leftovers of rosin flux agents from a PCB as soon as possible, by means of alcohol; I use the 99% alcohol
- Water-soluble or organic acid flux products. Lactic, citric and stearic acids combined with water and isopropyl alcohol are also quite effective for the use of electronics. Mainly, because they’re more powerful than rosin-based fluxes. It’s easier to clean PCBs after the use of organic flux agents. These products are electrically conductive and provide better performance rates;
Using Flux on a Circuit Board
My favorite flux, the one I use the most, is the ChipQuik SMD291 No-Clean Flux. It comes in a syringe, and is super easy to work with. It is in a more liquid form which makes it easy to dispense, unlike the thicker, pasty flux.
You only need a small amount, so, I use a needle to put it on the very small parts of my circuit board. It is non-corrosive, non-conductive so you don’t need to clean it off the PCB after use.
** I even use the SMD291 to re-hydrate the solder paste when we are making PCB panels to put in the reflow oven.
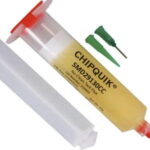
What flux agents you must avoid:
- Inorganic acid flux agents are good for bonding strong metals like stainless steel or brass. These agents include strong acids like zinc chloride or ammonium chloride. A complete cleaning is necessary immediately after using the soldering flux of this kind. The corrosive leftovers on the surfaces may destroy the solder joint! Never use such agents for assembling electronic devices or any electronic work;
- Lead-free electrical solder will do only for small wiring projects. Yes, such products are eco-friendly because have no lead but won’t make a strong hold;
Most experts advise picking rosin-based flux agents for electrical soldering. Most electronics and wires are extremely fragile, corrosive agents must be avoided. Local hardware stores will surely have such agents for soldering fans.
Consider using the so-called water-soluble fluxes. You can find them both in a liquid form and a semi-liquid gel. Their major advantage is a strong corrosive effect with maximum oxidation of the intertwined parts. Also, they don’t conduct electricity nor require washing the board after finishing the works. Nevertheless, it’s still better to remove all residual flux from soldered parts after soldering.
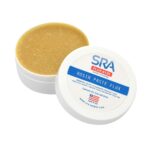
To apply liquid flux, you may require a paintbrush, cotton swab or even a single match. But it’s more acceptable to buy the so-called “flux applicator”. Branded flux applicators cost about $20-30 per item, so for some it will be a wiser choice to do such an applicator on their own. You will require a piece of silicone/rubber hose (choose the diameter of 5-6 mm), and a disposable syringe.
Apply a small amount of flux gel or paste to both parts being soldered. Put solder on the iron tip then put the solder iron on both parts. The flux will smoke as it melts and cleans the surfaces. Hold for a few seconds, then you should see a shiny solder once the parts are joined.
Put the cap on the flux when storing, so that the tip needle does not dry out, thin wire can be inserted inside it.
Consider using a no-clean flux gel or paste. For its application, you can also pick a disposable syringe, only because of its density, the syringe needle must be thick.
How should you prepare a soldering iron?
When working with electronics, it is essential to clean it immediately after use. So make sure the iron is clean and only then turn it on. Plug in or turn on the iron and wait while it is heating up. When it’s hot, apply a damp sponge for cleaning the tip. Do not touch the hot end while cleaning!
I like to clean the soldering iron tip BEFORE each use, and leave solder on it when I’m done. This keeps a layer of solder on the tip to prevent air from oxidizing it while not in use.
Always leave the iron on the stand when the tool is on. The hot tip may start a fire if left unsupervised.
When the iron’s tip hot and clean apply a small amount of solder. Wipe away any access with a damp sponge. Such a technique is called “tinning” the iron, it prevents oxidizing when you work with electronics.
The application process will depend on what kind of low-melting composition is used:
- When using solders it’s necessary to dip a soldering iron into the body of the reagent and hook a small amount of solder;
- If a liquid ready-made mixture is used, it can be applied with a brush;
- When working with paste, it is required to apply it to the junction with a stick, a toothpick;
- Also, do not forget about cleaning the surface from oxidation;
Consider wearing special gloves made for leather to prevent burns when using soldering flux agents.
Soldering Wires with Flux – Step-by-Step
- Initially, be sure the surfaces of each each wire is clean;
- After stripping, apply a flux layer;
- Intertwine the wires to avoid any pointed ends;
- To melt the flux agent pressure onto one side of intertwined wires. When the iron is hot, press it against one section of the wires to heat up. Keep pressing the iron to the wires until the flux is melted, but before bubbles appear;
- In the end, be patient for the seam to harden – in a few seconds;
It’s impossible to connect the contacts without a special composition. Experienced soldering users suggest that beginners do the job without flux and see the result — the job will take much longer, the shock will quickly fall off. The best additional material for adhesion is pure tin. However, this is not a cheap metal and mostly it’s applied along with lead.
Tips for Soldering Electronics with Flux
- Don’t forget about using flux on the board;
- No-clean flux is a “no-no” for assembling cables – solvents won’t remove such agents;
- After the job, please remove flux with any store or DIY solvents. They must drain away from contact-insulating zones;
- Water and solvent should never go to the body of your connector. If it happens, use fresh solvent for flushing the leftovers in this area;
- It’s better to pick deionized water for removing any residues;
- Stay away from the solder flux fumes, they may lead to asthma and other serious healthcare problems, consider wearing a respirator or fume extractor when applying;
I can’t say that soldering with flux is simpler when you deal with electronics and cables. But in the end, thanks to the previous tips you’ll get a solid bond in a shorter time period. And, that is what you seek, right? Bonding electronics with or without flux agents – what is your choice?
How to Use Flux When Soldering Electronics FAQ
What is Flux in Soldering?
Flux is a pasty or liquid substance that helps in the soldering, and welding processes. It helps to keep the surfaces clean from oxidation and acts as a “magnet” that attracts the molten solder to the parts being soldered.
Most consumers have no idea what flux is and what it is for. Flux is necessary for soldering. Workpieces that are mechanically and electrically connected to one another are referred to as soldered. These can be various parts, such as wires that are connected on a stranded wire or components that are soldered on a circuit board.
The actual function of soldering is to fill in the gaps between the workpieces so that a mechanical, electrical, and thermal connection is created in this way.
The problem with practicing this activity is that the workpieces are exposed to air for a long time and thus oxidize. When the surface is heated, this property becomes even more apparent. The oxide layer prevents the desired connection between the workpieces. Only now does the flux come into play. This auxiliary substance is a chemical compound. With the help of this connection, no new oxide layer is created and the existing layer is removed.
How much Flux do you need for soldering?
You should only use a small amount of flux when soldering. The thicker paste flux melts in the heat and becomes a large puddle. The liquid tack fluxes are better because they don’t cause a big mess on your PCB.
Do you need Flux to Solder?
Yes. A flux is a substance added during soldering, which causes better wetting of the workpiece by the solder. It removes the oxides on the surface through a chemical reaction. The same applies to oxides that are created during the soldering process by the oxygen in the air.
For work on oxidized joining partners, acidic fluxes are used (soldering fluid based on hydrochloric acid, salicylic acid, acetylsalicylic acid, adipic acid, soldering grease). Residues of acidic flux must be removed as they lead to corrosion of the solder joint in the long term.
Why use flux when soldering?
The flux not only removes the oxidation but also is there to reduce the interfacial tension in order to create better and more durable solder joints. This auxiliary material ensures that the parts to be joined are held together before they are finally soldered. The flux guarantees a good solder connection.
Inside the solder wire there is at least one core that is filled with flux. If the solder wire comes into contact with the components during soldering, the solder melts, and the flux is released, i.e. it burns and evaporates. Of course, if the flux is burned it will no longer work.
For this reason, additional flux is used. As a rule, this must also be used in order to get an optimal soldering result.
It is advisable to treat the soldering surfaces beforehand with the appropriate flux, which creates a protective surface that prevents oxidation. With conventional hand soldering, there is enough flux in the soldering wire.
What type of flux is used for electrical soldering?
The choice of flux depends on whether you will clean the PCB after soldering/reflow and the type of electronic parts used. In this case, high-quality flux must be used to avoid any residue or rust.
Dirty parts to be joined require an acidic flux which must be cleaned off. As a result, there are differences in the dosage, so that flux is offered in tubes or even in canisters. The differences between the products are briefly explained here:
- Multipurpose flux can be used anywhere;
- Suitable for Zn-Al alloys;
- For stainless and high-alloy steel;
- For Ni and Cu hard solders.
Is flux necessary for soldering?
Yes, flux is required so that the workpieces are optimally wetted by the solder during soldering. A chemical reaction removes the oxides present on the workpiece surfaces or prevents the formation of new oxides during the soldering process.
Besides, the surface tension of the liquid solder is reduced so that the solder can lie cleanly on the workpieces. Conveniently, the flux is fed to the solder joint together with the solder. For this purpose, the tin solder is built up in the shape of a tube and the flux is embedded inside.
Remember, when processing tin solder, the flux must first be applied manually to the sheet metal parts in the area of the soldering point.
What is water-soluble flux?
From the very beginning, you should understand that this is not some kind of a special type of flux. It is the property of flux to be water-soluble. If you have such kind of flux, it means that you can clear it after the soldering process with water.
Nevertheless, it is necessary to mention that no ordinary water should be used. It is recommended to use distilled or deionized water. Some detergents can also be compatible with the type of flux you have. Thus, you need to check the specifications of flux.
Thanks for sharing the content. Soldering flux is actually activated with the help of the heat of the soldering operation to remove the last layer of oxidized metal so that the solder will wet the base metal and produce a good joint.
Hello, thanks for the comment.
I bought a flux when i opened it, it was hard as a rock. Do i melt it b4 using it?
Hi! I would recommend to melt it.
Glad to learn about the application of flux on soldering electronics. Thanks for sharing the blog Tom.
Hi. Can you help me? When we perform soldering process finish, our gold surface is deformed. Do you know some reason for this problem? Thanks
Hello, Thuan! Once the solder has flowed along the joint, and the metal surfaces have been heated sufficiently to join together, turn off the torch and let the gold cool. After a couple of minutes, quench it further in the water bath. Use copper tools to lower the gold slowly into the pickle bath, and wait a few minutes for most of the discoloring fire-scale on the surface to be removed. Remove the gold from the pickle, rinse in the water bath, and inspect. You may need to polish or file off excess solder or fire scale to achieve the appearance you desire.
Hi.i have a problem which I can not answer for this. When we do soldering process, the gold layer is deformed. Please advise me for this. Many thanks
Thanks for showing how to use flux when soldering electronics! My brother is an electrician and I’ve often seen flux in his tool box but never actually understood how it worked.
Thanks for sharing the content. Soldering flux is activated by the heat of the soldering operation to remove the last layer of oxidized metal so that the solder will wet the base metal and produce a good joint.
Hi, Chris! Thanks for your comment.